Why Rotomolding is the Preferred Choice for Heavy-Duty Applications
Why Rotomolding is the Preferred Choice for Heavy-Duty Applications
Blog Article
Rotomolding, short for rotational molding, has changed into a game-changer in the production world, especially as it pertains to producing high-quality, tough plastic products. That adaptable method can be used to create sets from commercial gear to consumer goods, giving unparalleled longevity and style flexibility. Over time, developments in Rotomolding have led to more impressive answers, which makes it an essential method for producing plastic items that endure the check of time and hard conditions.
What's Rotomolding?
Rotomolding is an activity that requires heating plastic resin in the shape, spinning it in multiple axes, and enabling the product to settle into the required shape. This effects in a hollow portion that is uniform, strong, and lightweight. The method itself is very effective, giving producers with the capability to create delicate and complicated styles which are equally cost-effective and robust.
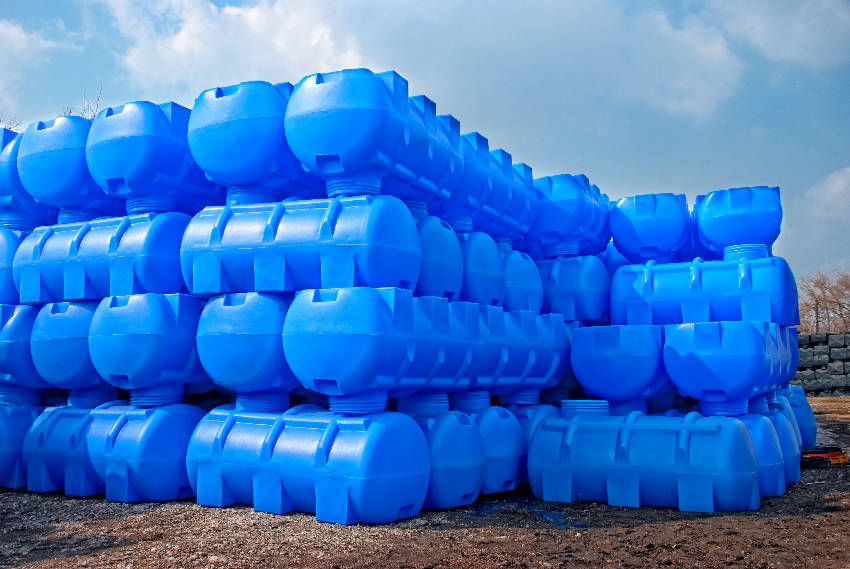
Crucial Benefits of Rotomolding
One of the main reasons for the rising recognition of rotomolding is their power to generate products which are resilient to use and tear. Unlike different plastic manufacturing methods, such as injection molding, rotomolding can generate smooth products and services without any joints, which considerably decreases the likelihood of weak points wherever cracks and problems may form. That smooth style makes rotomolded products perfect for outside and high-impact applications, including storage tanks, playground gear, and marine products.
The procedure also makes for freedom in item design. Whether it's an item with different wall thicknesses, specific color requirements, or custom patterns, rotomolding makes it possible to create precisely what is needed. That freedom means that companies can force the limits of design, building products that match specific functional and aesthetic requirements.
Sustainability and Performance
In addition to its durability, rotomolding presents substantial environmental benefits. The procedure produces little waste compared to different production practices, as any outstanding plastic may frequently be reused in potential production cycles. That, combined with the energy-efficient character of rotomolding, makes it a sustainable selection for producers looking to cut back their environmental impact.

Moreover, rotomolding creates products and services quicker and at a less expensive than a number of other methods. The paid down dependence on labor-intensive construction and the capacity to develop complex shapes within a stage decreases over all creation charges and reduces the time necessary for development. That efficiency makes rotomolding a nice-looking selection for industries which range from automotive to customer goods.
Realization
Rotomolding is revolutionizing the world of plastic manufacturing, offering impressive alternatives for making tough, resilient, and sustainable products. Its ability to create high-quality, complicated patterns with minimal waste and cost has managed to get a favored strategy in several industries. As technology continues to evolve, the possibility of rotomolding to create actually heightened and adaptable products and services is only going to increase, driving growth and advancement in several sectors. Whether for professional or daily applications, rotomolding is shaping the ongoing future of plastic solution design with resilience and ingenuity.
Report this page