The Science Behind Rotomolding: A Seamless Manufacturing Process
The Science Behind Rotomolding: A Seamless Manufacturing Process
Blog Article
Lately, rotational molding has acquired substantial grip on earth of manufacturing. As industries find successful, cost-effective, and versatile creation strategies, rotational molding has surfaced as a trusted alternative for making high-quality plastic products. This unique method, which requires Plastics Rotomolding while it is heated, enables manufacturers to generate services and products with complicated designs and uniform thicknesses, which makes it a great choice for a wide variety of applications.
What Makes Rotational Molding Stand Out?
Rotational molding, also called rotomolding, presents numerous advantages around different manufacturing techniques. Among the key factors causing its growing popularity is its cost-effectiveness. Compared to strategies like shot molding, rotomolding uses easy and economical conforms, which makes it a perfect choice for both small-scale and large-scale generation runs.

The method also allows for the manufacturing of useless parts and delicate styles that would be difficult or even impossible to reach with traditional methods. The ability to produce parts with varying wall thicknesses adds to the overall energy and toughness of the merchandise, which makes it perfect for industries where quality and resilience are essential.
Usefulness Across Industries
Yet another reason behind the rising reputation of rotational molding is its versatility. It's found in a diverse array of sectors, from automotive and agriculture to toys and outside equipment. Manufacturers can make from large storage tanks and watercraft to smaller, detail by detail components like medical devices and consumer goods. That freedom in style helps it be a go-to selection for industries seeking to create tailored, resilient, and modern products.
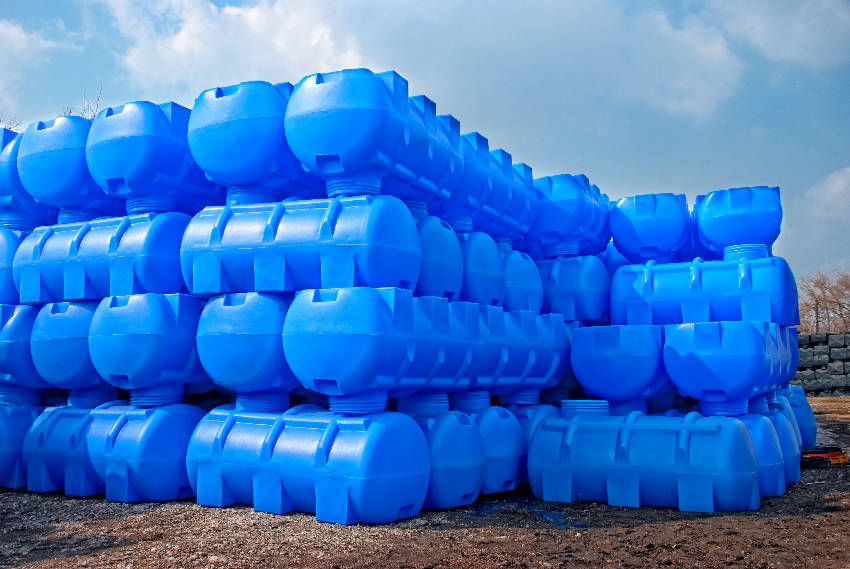
Sustainable Manufacturing
Rotational molding can also be increasingly recognized because of its eco-friendly qualities. It can be an energy-efficient process that produces small waste compared to different plastic manufacturing techniques, aiming with the rising emphasis on sustainability in modern production.
Conclusion
The increase of rotational molding in modern production is just a testament to its many benefits—cost-efficiency, design usefulness, toughness, and sustainability. As industries continue steadily to evolve, this innovative method will certainly enjoy a vital position in shaping the continuing future of plastic product manufacturing. Report this page